Exploring Rapid Plastic Prototyping: Transforming Metal Fabrication
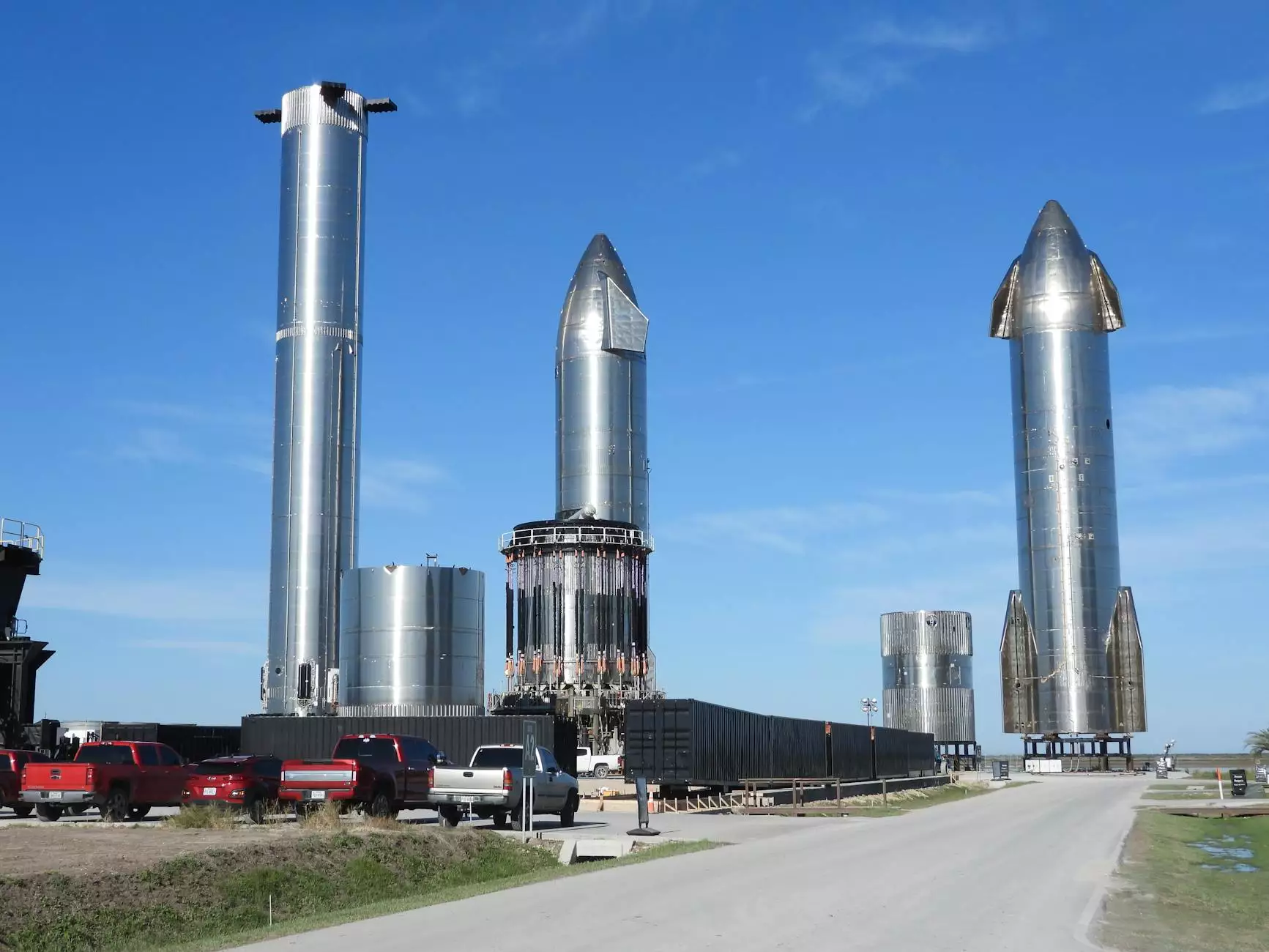
Rapid plastic prototyping has emerged as a game-changer in the manufacturing sector, specifically within the realm of metal fabrication. This innovative approach allows for quicker and more efficient production processes, significantly reducing the time from concept to market. In this article, we will dive deep into the nuances of rapid plastic prototyping, explore its myriad benefits, and understand its role in advancing the capabilities of metal fabricators, such as those at deepmould.net.
The Fundamentals of Rapid Plastic Prototyping
At its core, rapid plastic prototyping refers to the methods used to quickly create a scale model of a physical part or assembly using 3D computer-aided design (CAD) data. This process typically involves additive manufacturing techniques, such as 3D printing, which are integral for rapid product development.
Key Advantages of Rapid Plastic Prototyping
Implementing rapid plastic prototyping presents numerous advantages for businesses in the metal fabrication industry:
- Speed: The primary benefit of rapid prototyping is the significant reduction in development time. Compared to traditional prototyping, products can go from design to physical model in a matter of hours.
- Cost-Effective: By streamlining the prototype process, businesses can save on material costs and labor, allowing for better allocation of resources towards product refinement and marketing.
- Complexity Handling: Rapid prototyping can reproduce complex geometries that would be difficult or impossible to achieve using traditional fabrication methods.
- Iterative Design: This method allows for multiple iterations of a design to be tested rapidly, leading to enhanced product quality and innovation.
- Reduced Waste: Since prototypes are built layer by layer, waste is minimized compared to traditional subtractive methods. This makes it a more environmentally friendly option.
Applications of Rapid Plastic Prototyping in Metal Fabrication
The applications of rapid plastic prototyping are vast and varied, empowering metal fabricators to redefine their workflows:
1. Aerospace and Automotive Industries
In the aerospace and automotive sectors, where precision is paramount, rapid plastic prototyping is used to create highly detailed models for testing aerodynamics and ergonomics before mass production. Components such as brackets, housings, and enclosures can be prototyped quickly to evaluate their fit and function.
2. Consumer Products
Consumer product companies leverage rapid plastic prototyping to bring innovative designs to life. From gadgets to household items, the ability to create prototypes quickly enables designers to gather user feedback and iterate on designs, resulting in products that meet consumer demands effectively.
3. Medical Devices
In healthcare, designing medical devices with the utmost accuracy is crucial. Rapid prototyping allows engineers to build and test prototypes for equipment like surgical instruments and implants, ensuring they meet regulatory requirements and patient needs efficiently.
Technologies Behind Rapid Plastic Prototyping
Several technologies contribute to the success of rapid plastic prototyping. Understanding these technologies is vital for metal fabricators seeking to adopt this innovative practice:
- Stereolithography (SLA): Utilizes a laser to cure liquid resin into hardened plastic. SLA is known for its high accuracy and detailed finish.
- Fused Deposition Modeling (FDM): Involves extruding thermoplastic filament to create parts layer by layer, making it accessible and cost-effective for many manufacturers.
- Selective Laser Sintering (SLS): A process that uses a laser to fuse powdered materials, creating durable prototypes suitable for functional testing.
- Digital Light Processing (DLP): Similar to SLA but uses a digital light projector to cure resin faster, making it ideal for high-volume outputs.
Impact on the Metal Fabrication Industry
The integration of rapid plastic prototyping into metal fabrication practices has significant implications:
1. Enhanced Collaboration
With rapid prototyping, designers and engineers can collaborate more effectively. The production of tangible prototypes facilitates clearer communication of ideas and specifications, helping teams to align quickly.
2. Shortened Lead Times
Metal fabricators reduce lead times by utilizing rapid plastic prototyping to identify potential manufacturing issues early in the process, allowing for adjustments before final production.
3. Innovation and Customization
The ability to prototype rapidly encourages innovative designs and allows for customized solutions tailored to specific client needs, enhancing customer satisfaction and market competitiveness.
Challenges and Considerations in Rapid Prototyping
Despite its numerous advantages, implementing rapid plastic prototyping within metal fabrication comes with challenges that need to be addressed:
- Material Limitations: Not all materials can be used for prototyping. It is crucial to select the right material that aligns with desired properties and final production needs.
- Skill Requirements: Employees must be trained in both design software and the specific prototyping technology being used, which can require initial investment in training.
- Initial Setup Costs: While rapid plastic prototyping can save money in the long run, the initial capital required for machines and software can be substantial.
Future Trends in Rapid Plastic Prototyping
The future of rapid plastic prototyping holds exciting prospects for the metal fabrication industry:
1. Advancements in Materials
Innovations in materials, such as biodegradable plastics and composites, will enable more sustainable prototyping practices, aligning with broader environmental goals.
2. Increased Automation
As technologies evolve, automation in rapid prototyping is expected to increase, further reducing human error and enhancing production efficiency.
3. Expansion of Digital Twin Technology
The future may see the widespread use of digital twins, where a digital replica of physical assets is created to simulate performance. This can lead to even more effective testing and prototyping processes.
Conclusion: Embracing Rapid Plastic Prototyping for Success
In conclusion, rapid plastic prototyping is not just a trend; it is a vital component of modern metal fabrication practices that offers unparalleled benefits. Embracing this approach allows businesses, such as those at deepmould.net, to innovate rapidly, reduce costs, and improve product quality. By understanding its applications, technologies, and potential challenges, manufacturers can navigate the future of production with confidence and adaptability. The journey of continuous improvement through rapid plastic prototyping is indeed an exciting path that holds the key to competitive advantage in the ever-evolving marketplace.