Understanding Die Casting Production: A Key Player in Metal Fabrication
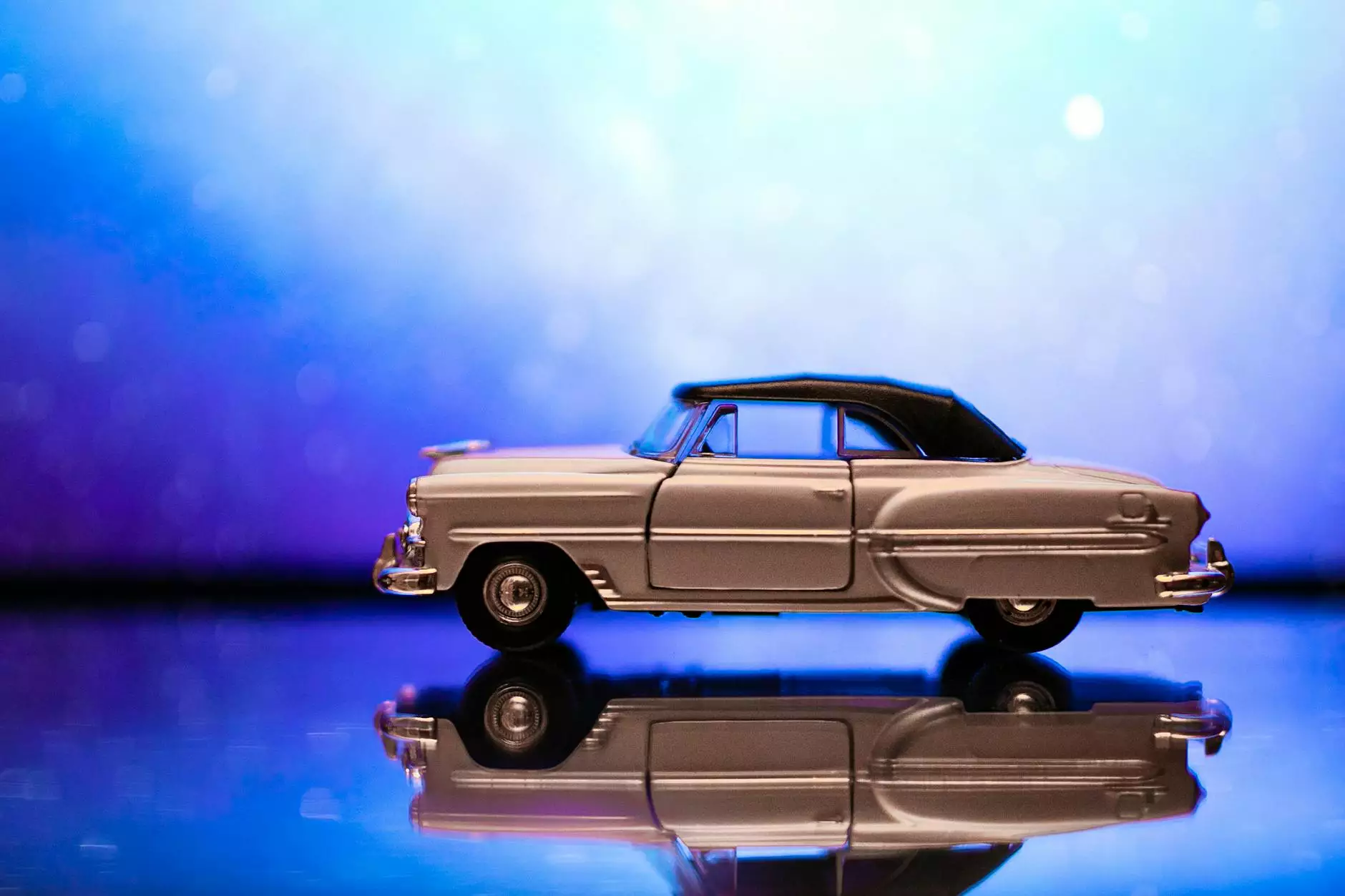
Die casting production is an essential methodology in the realm of metal fabrication, known for its ability to create complex shapes with precision and efficiency. This process plays a crucial role in various industries, including automotive, aerospace, and consumer goods. In this comprehensive guide, we will delve deep into the die casting production process, its benefits, and the reasons why it stands out in the metal fabrication sector.
The Basics of Die Casting Production
At its core, die casting production involves the injection of molten metal into a mold cavity. This method is particularly valued for its:
- High Precision: Molds are designed to very tight tolerances, ensuring that the final products meet exact specifications.
- Complex Geometries: The process allows for intricate designs that can be difficult or impossible to achieve through traditional machining methods.
- Fast Production Rates: Once a mold is created, reproducing parts can be done rapidly, making it ideal for mass production.
The Die Casting Process Explained
The die casting process can be broken down into several key steps:
- Mold Design: A mold is created based on the design specifications. This mold is typically made from hardened steel or iron.
- Melting the Metal: The chosen metal, often aluminum, zinc, or magnesium, is melted in a furnace.
- Injection: The molten metal is injected into the mold at high pressure. This pressure helps to fill the mold completely, preventing defects.
- Cooling: Once the mold is filled, the metal is allowed to cool and solidify, forming the final part.
- Mold Removal: After cooling, the mold is opened, and the casting is removed.
- Finishing: Additional finishing processes, such as machining, coating, or polishing, may be required to achieve the desired specifications.
Types of Die Casting Methods
There are two primary methods of die casting production:
1. High-Pressure Die Casting
High-pressure die casting is the most common method used in the industry. In this method, molten metal is injected into the mold at extremely high pressure, ensuring a quick fill and excellent surface finish. It's ideal for high-volume production runs.
2. Low-Pressure Die Casting
Low-pressure die casting utilizes a lower injection pressure. This method results in a slower fill time but allows for better control and less turbulence in the metal flow, making it suitable for larger or thicker castings where precision is still required.
Advantages of Die Casting Production
Die casting production offers numerous advantages, making it a preferred choice for manufacturers:
- Cost-Effective: In comparison to other manufacturing processes, die casting can be more cost-effective, especially for large production runs.
- Quality and Strength: The castings produced are strong and durable, often requiring minimal finish machining.
- Material Efficiency: Die casting minimizes scrap waste, as the process is highly efficient.
- Versatility: It can be used with a variety of metals and alloys, catering to diverse applications.
- Short Lead Times: The process allows for rapid production, which is beneficial for meeting tight deadlines.
The Role of Die Casting in Various Industries
Die casting production is integral to several key industries:
1. Automotive Industry
In the automotive sector, die casting is widely used for parts like engine blocks, transmission cases, and structural components. The ability to produce lightweight yet strong parts contributes to improved fuel efficiency.
2. Aerospace Industry
Die casting is also crucial in aerospace manufacturing, where precision components are essential. The aerospace industry benefits from the high strength-to-weight ratio provided by die-cast aluminum and magnesium parts.
3. Consumer Electronics
The consumer electronics industry relies on die casting for housings and structural components. The aesthetic finish and durability of die-cast parts are vital in this competitive market.
Quality Control in Die Casting Production
Quality control is paramount in die casting to ensure that the parts produced meet stringent specifications. Various techniques are employed, including:
- Dimensional Inspections: Regular checks are made to verify that the dimensions of the cast parts are within tolerances.
- Non-Destructive Testing (NDT): Methods such as ultrasonic testing or X-ray inspection can detect internal defects without harming the part.
- Surface Inspection: Visual inspections and advanced imaging technology assess the surface quality of the cast parts.
The Future of Die Casting Production
The die casting industry is on the brink of significant advancements. Innovations include:
- 3D Printing of Molds: The integration of 3D printing technology in mold fabrication could greatly reduce lead times and costs.
- Advanced Alloys: Research into new metal alloys is paving the way for even stronger and lighter die-cast components.
- Sustainability Practices: With increasing environmental regulations, die casting companies are focusing on recycling metals and reducing energy consumption during production.
Why Choose DeepMould for Die Casting Production?
At DeepMould.net, we understand the significance of high-quality die casting production. Here’s why you should choose us:
- Expertise: Our skilled professionals boast years of experience in die casting and metal fabrication.
- State-of-the-Art Technology: We utilize the latest equipment and techniques for superior die casting production.
- Customized Solutions: We work closely with clients to provide tailored solutions that meet their specific needs.
- Commitment to Quality: We uphold stringent quality control measures to ensure that every part meets your specifications.
- Timely Delivery: Our efficient production processes guarantee timelines are adhered to.
Conclusion
In conclusion, die casting production is a cornerstone of metal fabrication, widely appreciated for its efficiency, precision, and versatility. Understanding its processes and applications can help businesses leverage its benefits effectively. Whether you are in the automotive, aerospace, or consumer goods industry, embracing die casting can enhance product quality and production efficiency. Choosing a reliable partner like DeepMould ensures you achieve high standards in your manufacturing processes. For more information on our services, visit DeepMould.net.